エアバス社の誇る超大型機A380は、世界初の総2階建ての客席と最下層の貨物室をあわせ、3層構造を持つ巨大な旅客機です。これほどの機体を実現するためには、強さと軽さを非常に高いレベルで兼ね備えた、画期的な構造部材が必要でした。
2002年、エアバス社から届いた報せは、それらの開発を当社に依頼するものだったのです。
旅客機が飛ぶ10,000m上空の気圧は約0.2気圧と低く、乗客はこの低すぎる気圧に耐えることはできません。
そのため機内は約0.8気圧程度に与圧されているのですが、この機外と機内の圧力差によって、機体の構造材には膨らもうとする力が働きます。
その力は1平方メートルあたり実に6トンにもなるため、航空機にはこれに耐えるための材料や設計が必要なのです。
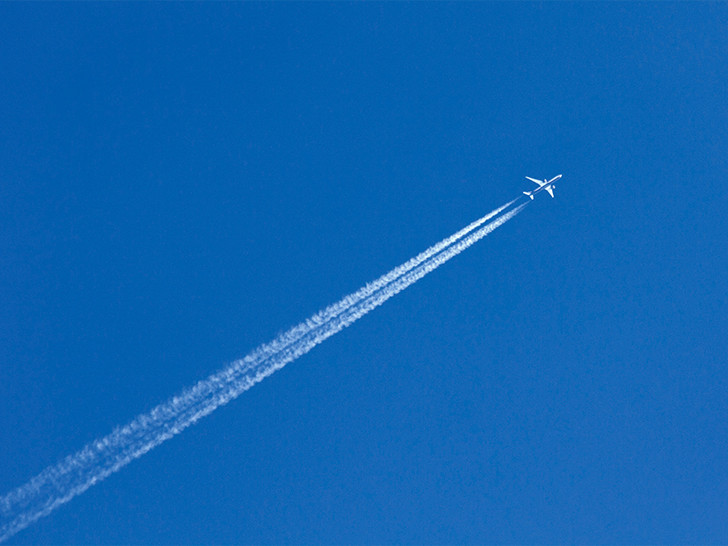
A380の場合、これまで一般的に使われてきたアルミ合金(ジュラルミン)を使った設計では重くなりすぎることから、機体構造の25%に、炭素繊維をエポキシ樹脂で固めた、軽くて頑丈な複合材料を使用しています。
これにより従来設計に対して大幅な軽量化に成功するのですが、この複合材料を用いた部品のうち2種類が当社開発品になります。
それが、垂直尾翼を支える構造材であるストリンガー、2階客席の床を支える梁の役割を果たすクロスビームです。
それまでの炭素繊維複合品の製造方法は、熱硬化性樹脂を含浸させた炭素繊維のシート(プリプレグ)を金型に積層し、それをオートクレーブという加圧オーブンで加熱して硬化させるのが一般的でした。
しかしこの方法では金型とオートクレーブが非常に大きく高コストなものになり、製造時間も長くかかってしまいます。
そこで当社は以前より、オートクレーブなどの大掛かりな設備を使わずに大型部品を製造するための製造法を独自に研究していました。それが脱オートクレーブ成形法であるアドバンスドプルトリュージョン、ADP製法です。
ADP製法の開発に成功した当社は、エアバス社からスティフナー、ストリンガーと呼ばれる垂直尾翼の一次構造部材の製造を受注しますが、その実績を認められてA380用の二階床構造部材、クロスビームの製造も依頼されることになります。
ストリンガーについては支給図面をそのまま製造する案件でしたが、それまでに前例のないサイズのクロスビームについては設計段階からの開発が求められます。
強度計算をしながらの部品設計と製造方法そのものの検討が必要だったためです。
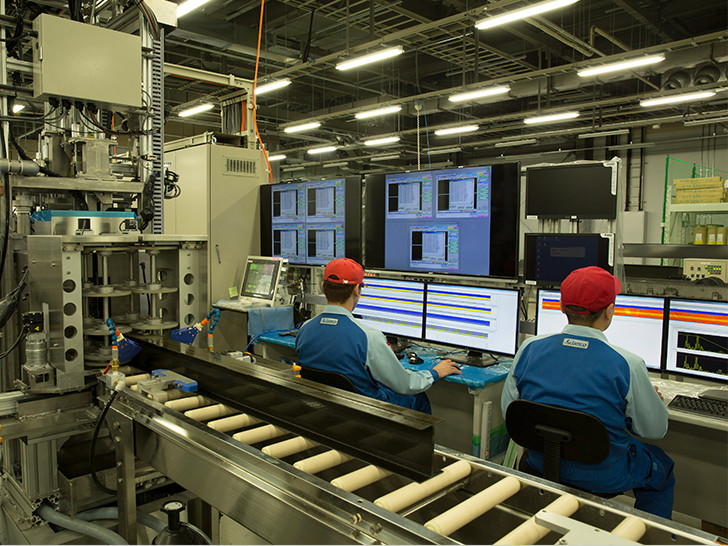
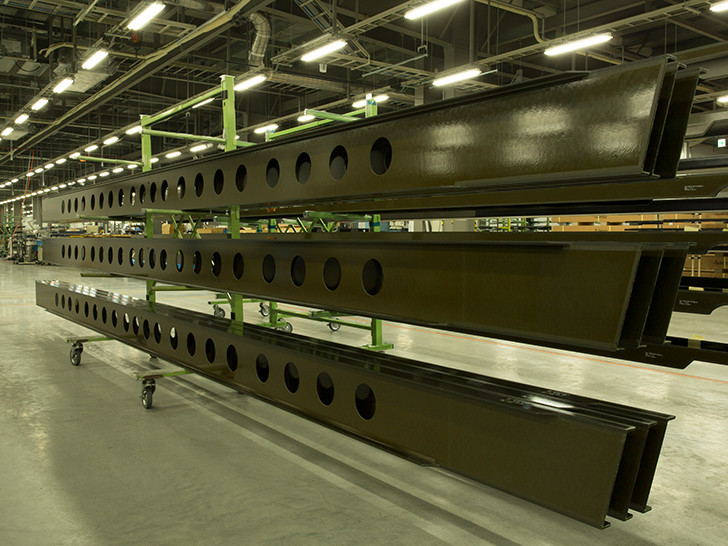
当社が開発したADP法は巨大な金型を必要としません。これは材料を短い金型の中を移動させながら成形する方式による利点です。
リールに巻かれた数枚のプリプレグを金型を通す際に圧縮、加熱することにより、理論的に長さ制限のない部材の製造が可能な上、真直性や直角度についても高い精度を確保できる仕組みです。
この製法により、それまでとは比較にならないスピードで大型部品を作ることが可能になり、大幅なコストダウンも実現することができました。
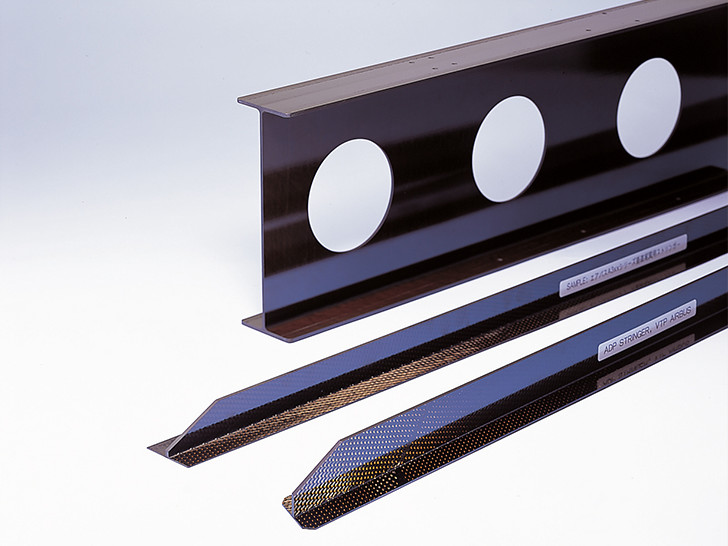
また、オートクレーブ製法での使用を前提とした既存のプリプレグは、ADP製法では最高のパフォーマンスを発揮できないため、材料も炭素繊維メーカーと共同で開発した最適なプリプレグを使用しています。
このようにして、設計、材料、製造法のすべてをA380のために最適化して作られたクロスビームは、1本7mの大型部品でありながら15kg程度しかなく、女性一人で持ち上げることが可能なほど軽量に仕上がると同時に、並外れた強度が要求される航空機用構造材の規格をも満たすことに成功したのです。
- 拡大
- 写真提供:エアバス