

JAMCO Group is leveraging its expertise in special process techniques to manufacture jet engine parts, Carbon-Fiber-Reinforced plastic (CFRP) carbon-fiber structural members, and other aircraft components at a high level of quality and safety.
Leading Proprietary Technologies, Including a Patented Continuous Molding Method for Carbon-Fiber-Reinforced Plastic (CFRP) |
Operations Certified by Nadcap, a Global Standards Accreditation Program |
JIS Q 9100 Certification, a Quality Management System Required by Manufacturers in Japan's Aerospace Industry |
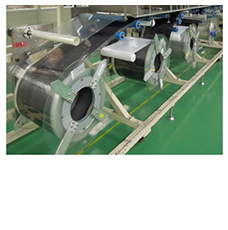
JAMCO’s special process techniques can be applied continuously by means of automation, allowing it to mold members for a theoretically unlimited amount of its length. Compared to conventional methods, JAMCO’s techniques enable parts and components to be manufactured over shorter periods and at lower costs. Moreover, it’s excellent internal molding quality, delivers extremely high accuracy, such as straightness.

Since April 2014, JAMCO Group has been accredited by Nadcap, an international accreditation program for special processes in the aerospace industry, for three processes: Nondestructive testing (NDT), Composites (Composites), and Laser machining (NM).
JAMCO has obtained JIS Q 9100 certification for its aircraft components manufacturing operations. JIS Q 9100 is a quality management system required by manufacturers in the aerospace and defense industries in Japan, and is equivalent to the AS 9100 standard used in North America and the EN 9100 standard in Europe.
JAMCO’s CFRP adopted in TAISEI CORPORATION’s vibration/sound-proofing structure frame “T-Silent® CFRP Frame”
- 拡大
- Photo Providing:TAISEI CORPORATION
JAMCO’s CFRP (carbon-fiber reinforced plastic) made with ADP process was adoptedby TAISEI CORPORATION’s vibration/sound-proofing structure frame “T-Silent® CFRP Frame,” demonstrating excellent workability.
ADP (Advanced Pultrusion) is a process developed by JAMCO for continuous manufacturing of CFRP. ADP has the characteristics that enable the manufacturing of parts without any limit to their length in theory and realize extremely high precision with respect to straightness and perpendicularity, among other things.
Various types of metals and composite materials are used to manufacture aircraft, and JAMCO processes those substances utilizing advanced techniques to meet the strict standards required in aerospace development. Moreover, the JAMCO Group’s manufacturing facilities maintain a stable supply of products, and ensure that they are airworthy by deploying a rigorous quality control system. As a result of these efforts, JAMCO has earned a strong reputation as a manufacturer of aerospace equipment. While paying meticulous attention to quality, JAMCO combines special process techniques—its core competency—and original design concepts to respond to the needs of customers and supply a wide range of aerospace equipment and products, including heat exchangers, civil aircraft engine parts, aerospace development devices and components, chassis for electronic equipment, and products made of high-strength and lightweight composite materials.
- 拡大
- Photo Providing : Japan Air Self-Defense Force
A key base for manufacturing CFRP structural members and engine parts in the JAMCO Group’s aircraft components manufacturing operations
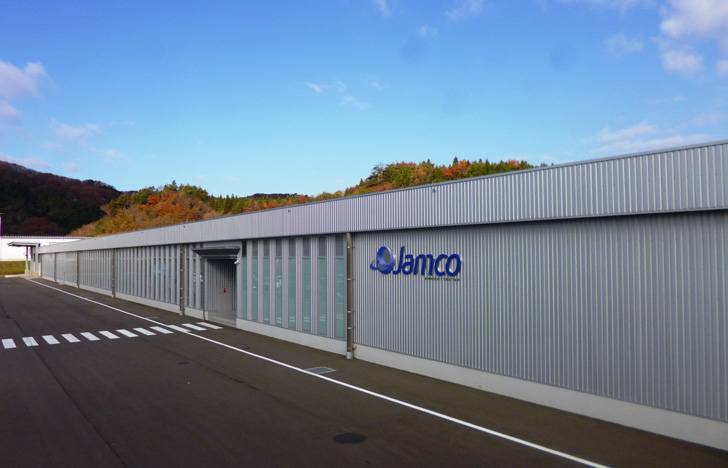
JAMCO AEROMANUFACTURING Co. Ltd.
Established on April 1, 2013 in Natori City, Miyagi Prefecture, as a company responsible for the production of aircraft engine parts and CFRP structural members.
JAMCO AERO MANUFACTURING Co., Ltd. is a key base in the JAMCO Group’s aircraft components manufacturing operations and celebrated its 10th anniversary on April 1, 2023.